Sustainable materials
At LAB Design, we are constantly seeking ways to offer our clients viable alternatives to the conventional, environmentally harmful plastics that dominate the market. Our approach starts with examining the full life cycle of materials—from production and usage to recycling through the lens of circular economy principles and sustainability.
Lifecycle of materials
While nearly all thermoplastics are technically recyclable with minimal degradation, only 9% of recyclable materials are actually processed according to data from OurWorldInData. The challenge lies not just in the material's recyclability, but also in the intricate processes required to convert discarded products into secondary raw materials. This complexity underscores the need for more effective recycling systems and sustainable design practices.

1. the life cycle of plastic materials
Recycling is the process of returning a material to an earlier stage. This can be done in different ways, using mechanical or chemical transformation methods. The choice between mechanical and chemical recycling depends on the type of plastic and the desired quality of the final products.
The illustration below demonstrates the different stages of these processes:

2. Recycling process of polymers
Chemical recycling
First, discussing the chemical recycling techniques: pyrolysis and gasification, which are widely used in the recycling of plastics, especially for materials that mechanical recycling struggles with, such as mixed and contaminated waste.
Pyrolysis:
Involves heating plastic waste (primarily polyolefins like polyethylene (PE) and polypropylene (PP)) in an oxygen-depleted environment, usually between 300-650°C.
Breaks down the polymers into simpler hydrocarbon molecules, typically producing pyrolysis oil and non-condensable gases.
It can process mixed plastic waste, even with contamination, making it suitable for plastic packaging, films, and bags. Particularly valuable in handling materials where mechanical recycling is ineffective, such as multi-material or multi-layered plastics.
Chemical Depolymerization:
Breaks down plastics into monomers or oligomers using chemicals under controlled conditions. The recovered building blocks can be reused or mixed with virgin monomers to produce new, virgin-grade polymers.
Best suited for pre-sorted, pure streams of plastics, which limits its application due to economic and technical constraints.
Gasification:
The plastic waste is heated at higher temperatures (500-1300°C) with limited oxygen, leading to the production of syngas (a mixture of hydrogen and carbon monoxide).
Syngas can be used as feedstock for various chemical processes, though it has been applied mostly for fuel production rather than direct plastic recycling.
While gasification has commercial applications in fuel production, its usage for converting plastic waste back into new plastics is less common compared to pyrolysis.
Mechanical recycling
Thermoplastics are a category of plastics that become moldable upon heating and solidify upon cooling. The recycling process for thermoplastics typically begins with the collection of post-consumer waste or post-industrial waste (scrap generated during manufacturing processes).
The plastic recycling journey involves many key steps:

3. Mechanical recycling process
-
Collection: Waste plastics are gathered from various sources, including residential recycling programs and industrial manufacturers.
-
Sorting: Once collected, materials are sorted to separate thermoplastics from other types of plastics and contaminants. This step is crucial to ensure high-quality recycled materials.
-
Pulverizing: After sorting, the plastics are pulverized into small pieces or flakes, making them easier to process further.
-
Mechanical Recycling: In this method, processed plastics are melted and reshaped into new products without altering their chemical structure.
Example I.
Electrolux ultraone green.
Together with Stena Recycling, Electrolux has developed a vacuumcleaner, made of 100% recycled and reused materials.
The plastic and components originate from consumers electronic products, such as used hairdryers, vacuumcleaners and computers.
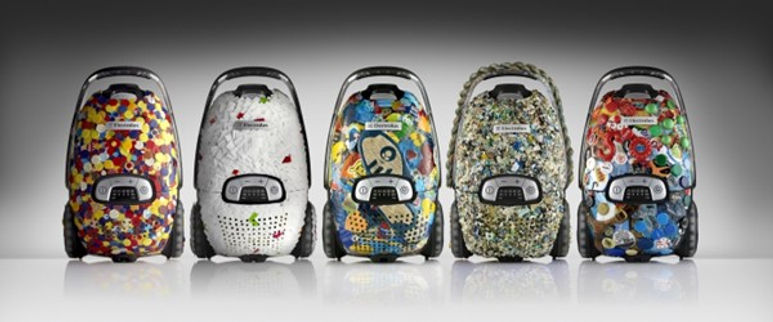
3. Mechanical recycling process
Bio-based materials
Recycling is only one part of the solution when it comes to sustainable plastic materials. Equally important is the production of the raw materials themselves. We believe that true sustainability begins with the materials we choose and how they are sourced.
​
Bio-based materials offer an eco-friendly alternative by incorporating plant-based ingredients in their production processes, which significantly reduces their overall carbon footprint. These materials are derived from biological sources, such as renewable agricultural resources, making them a key component of the shift towards a more sustainable design future.
Bio-based is defined as a material that comes, in whole or in part from “bio”, therefore living sources.
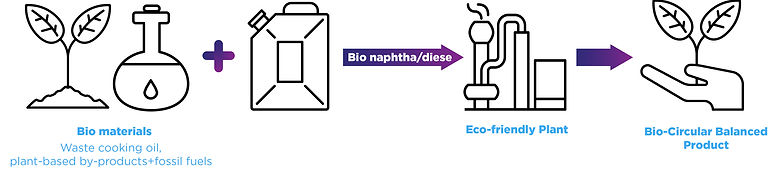
5. Bio-based material production process
The bio-based renewable feedstock, produced from bio-based renewable oil, is blended with fossil-based oil to reduce carbon emissions during the manufacturing process.
​
It is crucial to distinguish bio-based plastics from the term "biomaterial."
Bio-based refers to the composition of the material, meaning it includes biological origins, but this does not automatically mean the plastic is biodegradable. That means, not all bio-based plastics will break down naturally in the environment.
Some bio-based plastics can be recycled using traditional plastic recycling processes. However, others are compostable, meaning they can break down under industrial composting conditions. It is important to differentiate between these two end-of-life pathways when considering the sustainability of bio-based plastics.
​
For bio-based plastics that are not suitable for recycling or composting, waste-to-energy processes can be an option. In this scenario, the CO2 emissions from incinerating bio-based plastics are often considered "neutral" because the carbon released during incineration was originally absorbed by plants during their growth.
Example II.
Philips Eco Conscious Edition Breakfast set
Waste cooking oil is now being added to the raw materials used to produce bioplastics, which already include beet molasses, sugar cane, fruit and potato waste, and crude glycerol. After treatment, the bioplastic produced has the same qualities as those made from other agro-industrial by-products. Philips has come up with the world’s first breakfast set made with 100% Bio-based plastics from used cooking oil. Not only the products but also the pacaging themselves were designed with sustainability in mind.


Philips Eco Conscious Edition
https://www.philips.com.hk/en/c-e/ho/cooking/eco-conscious-edition.html
If you’re interested more of our thinking and strategies of industrial products, contact us and we are happy to support you and your organization.